Common Printing Techniques for Packaging Materials
Four-Color Printing (CMYK)
1. The term "four-color" refers to the use of four inks: Cyan (C), Magenta (M), Yellow (Y), and Black (K). All colors can be created by mixing these four inks, ultimately producing full-color images and text.
2. This is the most basic and common printing method, with different results depending on the substrate used.
Pantone Color Printing
1. Pantone color printing uses a specific, custom-mixed ink to print a particular color, resulting in a more vibrant hue than what's achievable with four-color mixing. Common spot colors include metallics like gold and silver.
2. Pantone colors are available in a wide range, as referenced in Pantone color guides. Pantone colors cannot produce gradients; if needed, four-color printing is added.
UV Coating
1. UV coating enhances specific areas of a printed material by applying a glossy finish, making certain designs or text appear more three-dimensional.
2. This technique is typically combined with matte lamination; it does not produce any effect when used with gloss lamination.
Hot Stamping
1. Hot stamping uses heat and pressure to transfer a metallic foil onto the substrate, creating a special metallic sheen on the surface.
2. Common colors for hot stamping include gold, silver, red, green, and blue. However, hot stamping is limited to a single color per application, and not all colors are readily available on the market.
Embossing
1. Embossing uses a pair of male and female dies to press a substrate, creating a raised (embossed) or recessed (debossed) design, giving it a tactile, three-dimensional effect.
2. This technique can be used on various paper thicknesses, though it is not suitable for cardboard.
Inkjet Coding
1. Inkjet coding involves using an inkjet printer to apply markings such as production dates, expiration dates, batch numbers, and company logos directly onto products.
2. It allows for the printing of simple characters and designs with greater flexibility.
Composite Bags
1. Composite bags are suitable for vacuum or general packaging of products like food, electronics, chemicals, pharmaceuticals, and tea.
2. They can undergo similar processes as paper, such as screen printing, regular printing, and hot stamping.
Blister Packaging
1. Blister packaging is made from transparent materials, primarily PVC, PP, or PET.
2. It can directly replace paper for box production or be used with cards to form shapes.
3. It can be used inside packaging to secure products, known as blister inserts.
4. Blister packaging can be screen printed, regular printed, or hot stamped.
5. It can be machine-printed, but the printing cost is high, so screen printing is generally used for small-scale production.
OPP Bags
1. OPP bags are made from oriented polypropylene, a type of plastic, essentially plastic bags.
2. Products are often placed in an OPP bag before being packed in an outer box to appear clean and hygienic.
3. Other materials include PP bags and PE bags.
4. OPP bags are characterized by high transparency and brittleness and can be printed with various designs or perforated according to customer needs.
EVA (Ethylene-Vinyl Acetate)
1. EVA is a copolymer of ethylene and vinyl acetate, and products made from it are known for their softness, shock resistance, anti-slip properties, and strong compression resistance.
2. It is used in packaging and interiors to secure and protect products.
3. EVA is available in various colors, and the surface can be flocked or wrapped in velvet to enhance visual appeal.
Foam
1. Foam is a porous material with excellent elasticity, with varying elasticity depending on the density of the pores.
2. It is used in packaging and interiors to secure and protect products.
3. Foam is available in various colors and is typically used directly without additional processing.
Common Packaging Materials
1. A common material for paper boxes, available in thicknesses ranging from 80g to 400g. For higher thicknesses, two sheets are glued together.
2. The paper has one glossy side and one matte side; only the glossy side can be printed on.
3. It allows for printing in any color without restrictions.
4. Common surface treatments after printing include lamination, UV coating, hot stamping, and embossing.
Corrugated Paper
1. Compared to regular paper, corrugated paper is stiffer and has better load-bearing capacity.
2. Common types include single-wall, double-wall, and triple-wall corrugation.
3. It allows for printing in various colors, though the result is not as refined as single-sided coated paper.
4. Common surface treatments after printing include lamination, UV coating, hot stamping, and embossing.
1. Used for making gift box structures, with a layer of single-sided coated paper or specialty paper laminated on top.
2. Common colors include black, white, gray, and yellow.
3. Paperboard comes in various thickness levels, chosen based on the required load capacity.
4. If laminated with single-sided coated paper, the processing techniques are the same as for single-sided coated paper boxes. If laminated with specialty paper, most can only be hot stamped, and some can be printed with simple designs, though the print quality is not as good.
Specialty Paper
1. There are many types of specialty paper; the ones used for packaging materials include embossed paper, textured paper, pearlescent textured paper, metallic textured paper, gold paper, etc.
2. These papers undergo special treatments to enhance the quality and luxury of the packaging. Embossed and textured papers cannot be printed on, but they can be hot stamped. Pearlescent and metallic papers can be printed using four-color printing.
1. UV transfer technology is used to apply a layer of UV oil onto the paper's surface via a rubber blanket, then specific patterns or holographic effects are transferred onto the paper, creating a radiant, holographic effect similar to laser paper.
2. Only UV printers can be used for printing on this material. It can achieve various patterns and effects, offering a more textured feel compared to regular paper, but at a higher cost.
BEP Packaging provides different packaging materials with different printing and finishing techniques. Welcome to contact us to customize the packaging.
YOU MAY ALSO LIKE
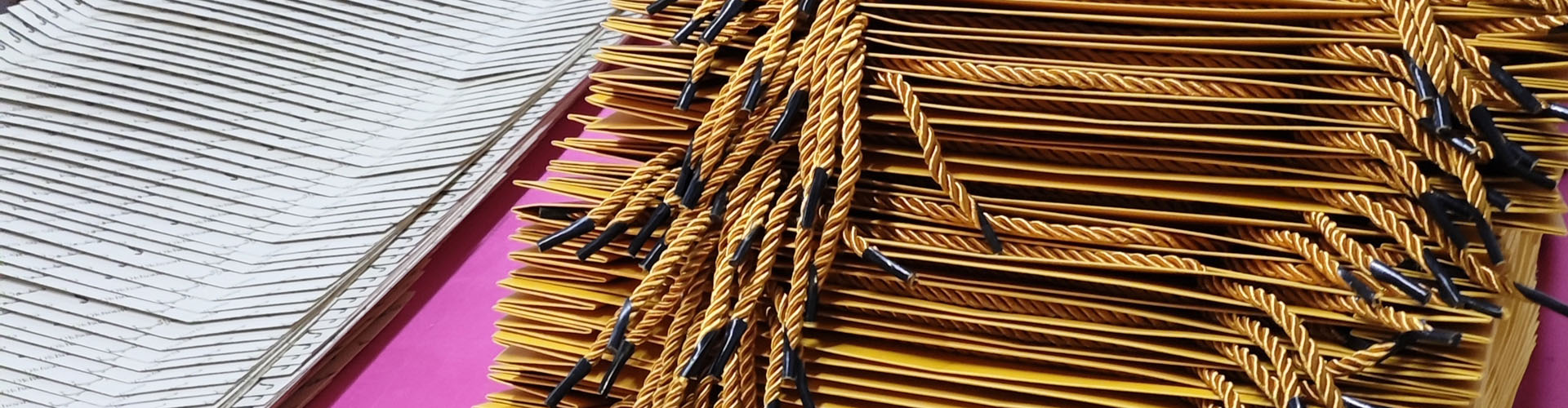
What is sustainable packaging
2023-05-05 02:03:21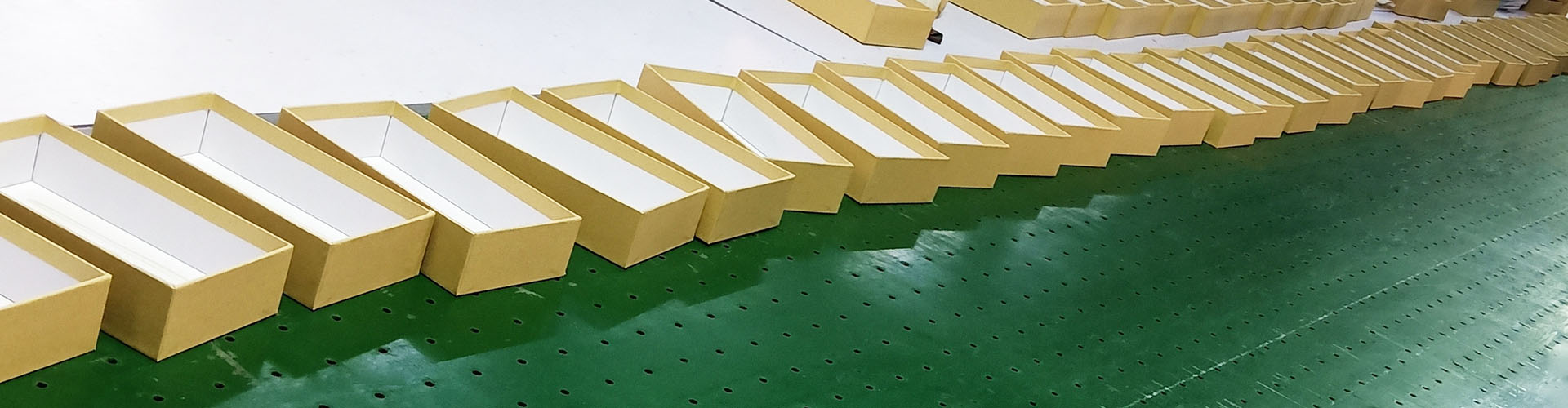
Customized Packaging Solutions with a Commitment to Sustainability
2023-07-15 07:23:59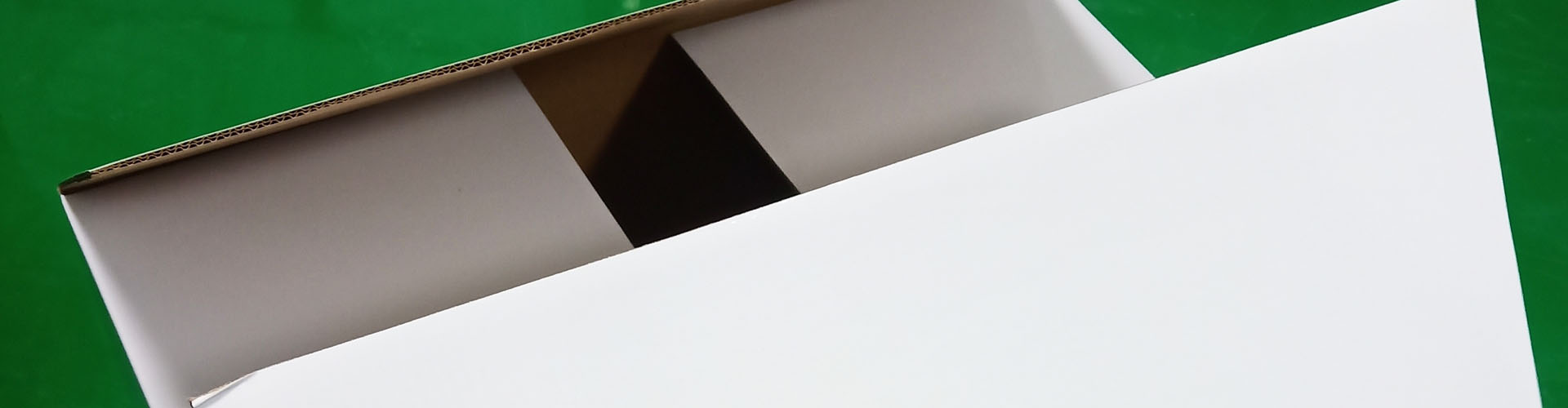
Reducing Waste and Increasing Recycling
2023-07-18 04:01:48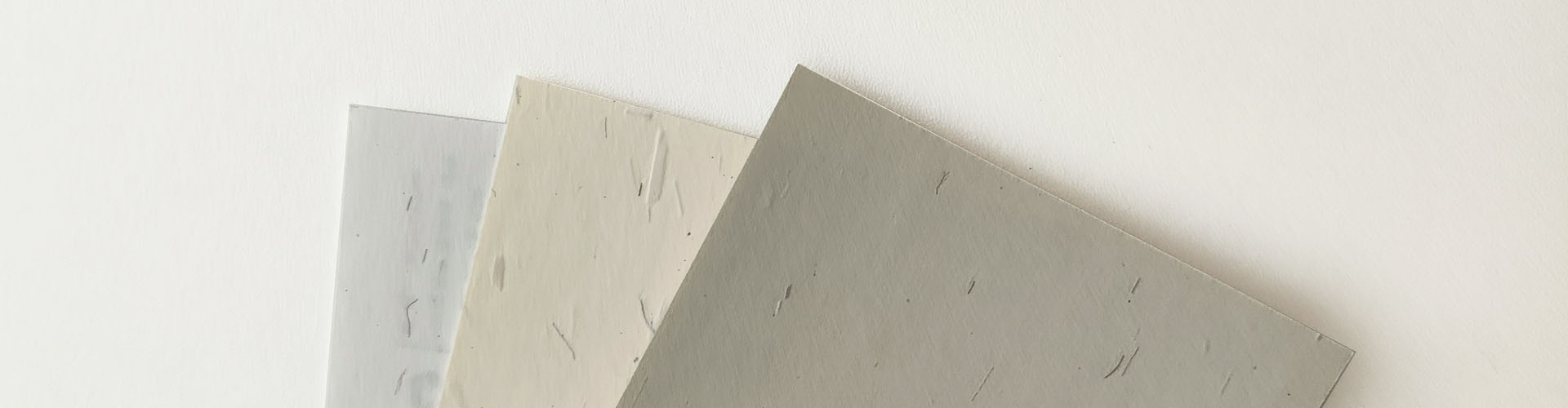
Promote sustainable practices throughout the supply chain
2023-07-18 06:35:56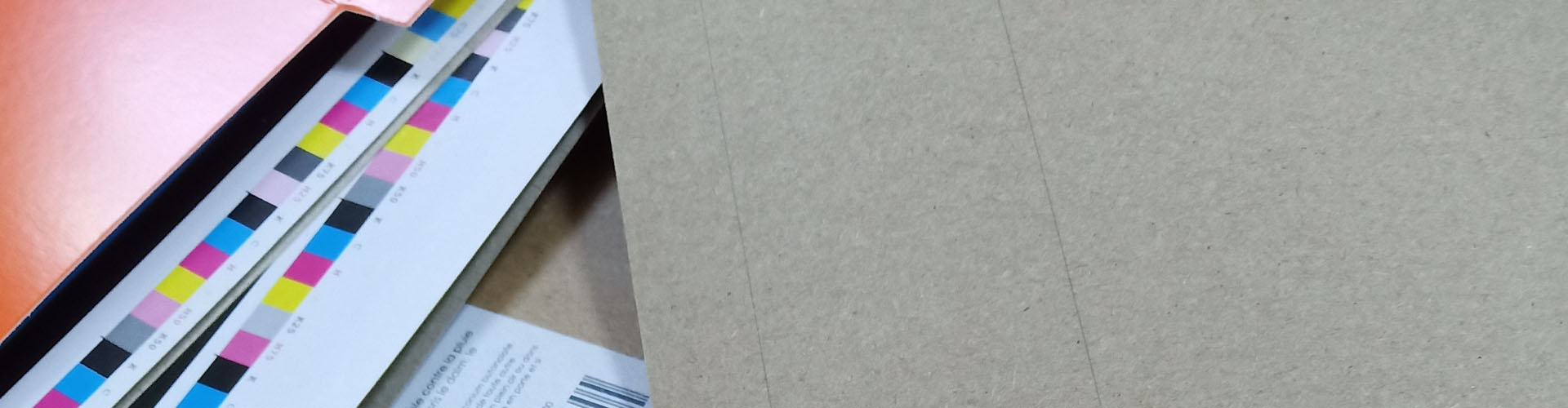
Focus on eco-friendly materials
2023-07-18 07:04:38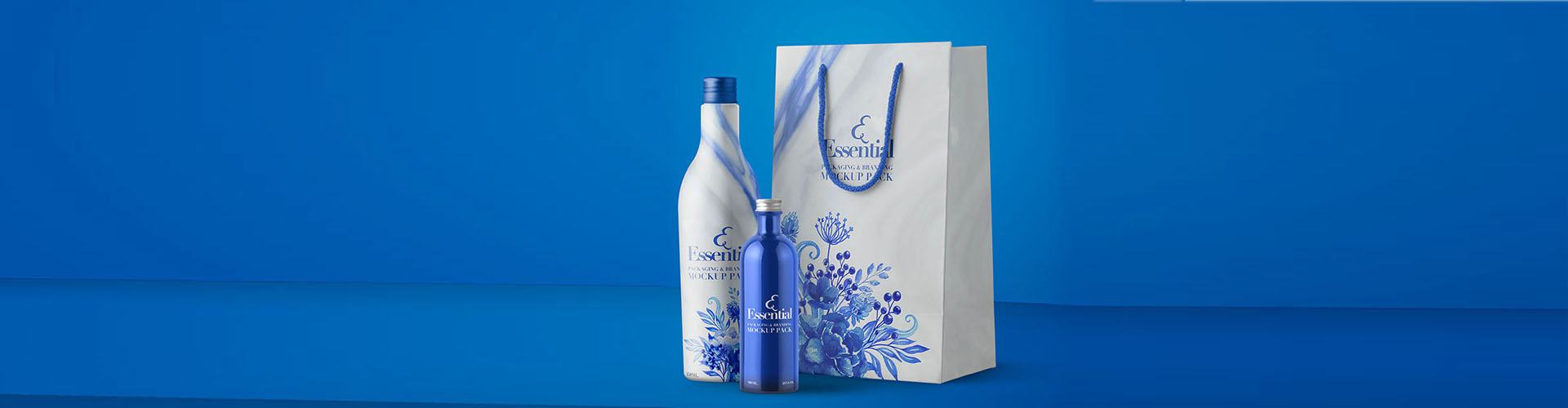
The packaging solution tailored for a specific product
2023-07-18 07:32:16POPULAR POSTS